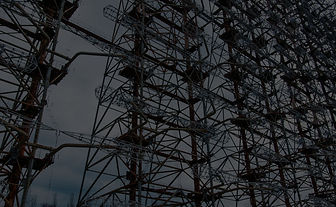
MS Scaffolding Towers: Safe and Sturdy Solutions for Construction Projects
MS Scaffolding Towers provide rapid, safe, and versatile access solutions for a wide range of construction, maintenance, and industrial applications. Engineered from high-grade mild steel and compatible with both H-frame and Cuplock systems, Avanza Steel’s towers are fully portable, lockable, and extendable up to 8 meters, making them the ideal choice for contractors who demand efficiency without compromising on safety.
What Is an MS Scaffolding Tower?
An MS Scaffolding Tower is a mobile working platform assembled from prefabricated steel components—vertical frames, horizontal ledgers, cross braces, and deck planks—mounted on lockable castor wheels. Our towers can be configured using either:
-
H-Frame Modules: Welded H-section frames of 48.3 mm OD × 3.0 mm wall MS tubes (per IS 1161), offering simplicity and rapid setup.
-
Cuplock Modules: Vertical Cuplock standards and matching horizontal ledgers for tool-free, click-in assembly and adjustable bay widths.
Top Benefits:
-
Portability: Four heavy-duty swivel castors (with lockable brakes) allow single-person manoeuvres on flat surfaces.
-
Adjustable Height: Stackable modules extend platform heights in 0.5 m increments to a maximum of 8 m.
-
Modular Flexibility: Mix H-Frame and Cuplock components to suit project requirements.
-
Safety & Compliance: Engineered per BS EN 1004 and OSHA 1926.452 standards for mobile access towers, with integrated guardrails, toeboards, and ladder access points.
Component | Specification |
---|---|
Vertical Frames | H-Frame: 48.3 mm OD × 3.00 mm WT MS ERW per IS 1161
Cuplock Standard: 48.3 mm OD × 3.00 mm WT with welded cups every 0.5 m
|
Horizontal Ledgers | 48.3 mm OD × 3.00 mm WT MS tube; forged blade ends; load capacity 10 kN midspan |
Cross Braces | 25 × 25 mm × 2 mm MS angle; quick-fit couplers |
Deck Planks | MS Walkway Jaali or anti-skid MS Plank, 0.30 m width; load rating 200 kg/m² |
Castor Wheels | 150 mm diameter, nylon tread; load rating 300 kg per wheel; locking brake |
Platform Heights | 1.0 m, 1.5 m, 2.0 m, ... up to 8.0 m (stackable in 0.5 m increments) |
Guardrails & Toeboards | 1.0 m high MS guardrails; 150 mm toeboards; clip-on design |
Finish | Industrial epoxy-dip paint (50 µm) or hot-dip galvanization (85 µm) |
Compliance | BS EN 1004:2004, OSHA 1926.452, IS 3696 |
Technical Specifications
Applications & Use Cases
-
Interior Fit-Out & Maintenance
Rapid, wheel-mounted towers allow seamless transitions between work areas in warehouses, factories, and retail spaces.
-
Facade Works & Painting
Smooth adjustment and guardrail systems provide safe perimeter access for plastering, painting, and glazing tasks.
-
Electrical & Mechanical Installations
Elevated platforms support cable tray fitting, pipe installations, and HVAC commissioning at heights up to 8 m.
-
Civil & Infrastructure Projects
Modular configurations serve as bridge abutment access towers, maintenance stands for underpasses, and inspection platforms for overpasses.
Installation & Best Practices
1. Site Preparation
-
Ground Check: Confirm a flat, level surface free of debris. For softer ground, use timber soleboards under wheel plates.
-
Component Inspection: Before assembly, inspect all tubes, couplers, and wheels for damage, corrosion, or deformation.
2. Tower Assembly
-
Base Module: Position two H-Frame or Cuplock uprights on castors, lock brakes.
-
Ledger & Brace Connection: Insert horizontal ledgers at the desired first lift height; secure cross braces diagonally for rigidity.
-
Deck Installation: Lay MS Walkway Jaali or MS Planks onto ledger ledges; clip to prevent movement.
-
Guardrail Fitting: Attach guardrails and toeboards on all open sides of the deck.
-
Subsequent Lifts: Add another module set atop the guardrail connections, repeating ledger, plank, and guardrail steps until desired height.
2. Dismantling & Mobility
-
Reverse Assembly: Remove deck boards, guardrails, ledgers in reverse order.
-
Brakes & Transport: Lock castors before moving; push tower from a low deck to avoid tipping.
Maintenance & Lifecycle
-
Daily Pre-Use Check: Ensure wheel brakes function, couplers are tight, and no components are visibly damaged.
-
Monthly Thorough Inspection: Check welds on H-Frame uprights, cup welds on Cuplock standards, and integrity of epoxy/galvanized finishes.
-
Lubrication & Cleaning: Wipe down tubes with a mild lubricant to prevent rust; clear dirt from castor axles for smooth rolling.
-
Lifecycle Management: Replace any tube or wheel showing > 10 % wear or deformation; maintain a record of inspection dates.
Elevate your access solutions with Avanza Steel’s MS Scaffolding Towers:
👉 Download the full Product Brochure for detailed part codes, dimensional drawings, and load charts.
👉 Contact our team at avanzasteel@gmail.com or +91 33 4000 7575 to request a site-specific quote, arrange a factory tour, or schedule an on-site technical consultation.
-
What makes Cuplock scaffolding faster than traditional tube-and-clamp?The cup-and-blade mechanism requires no loose bolts or nuts—each connection locks with a simple downward press, reducing assembly time by up to 40 % compared to tube-and-clamp systems.
-
Are Avanza Steel’s Cuplock standards compatible with other brands?Yes, our Vertical Cuplock standards and Horizontal Ledgers maintain a strict tolerance of ± 0.5 mm on cup dimensions and blade ends, ensuring cross-compatibility with any IS 12873‐compliant Cuplock systems.
-
How do I calculate the number of ledgers needed per level?Divide the total bay length by 0.50 m (cup spacing) to get the number of ledger connections. For instance, a 3 m bay requires six ledgers per level—plus one spigot pin above for extension continuity.
-
Can Cuplock scaffolding be used on curved façades?Yes. Swivel clamps in combination with half-meter cup spacing allow you to create curved geometries. We recommend a maximum curvature radius of 2 m to maintain load distribution and minimize component stress.
-
Where can I find detailed part codes and weights?Refer to our Avanza Steel Product Brochure (page 5–6) for the full list of Vertical Cuplock codes (AV-05 to AV-30), corresponding weights, and all complementary accessories.